FlexEdge
Back to overviewThrough years of experience and use of the latest technology, OTT guarantees a perfect finish of your edge banding with an extremely fine to practically invisible glue joint.
Simple operation via touch screen of both gluing system and the various processing units.
Thanks to the clear icons of the various units and the individual converters, the various units can be individually electro-pneumatically switched on and off and fine adjustment according to the sheet and edge material to be processed is possible from the control panel itself.
This avoids manual intervention on the units themselves.
With the unique CombiMelt system, both EVA and PUR adhesives can be processed.
Various parameters such as temperature, rotation direction of the glue roller, extremely precise dosing of the glue quantity can be adjusted according to the sheet and edge material to be processed.
The quick-change system for glue containers and glue rolls in combination with a specially developed 'storage box' for PU glue containers allows quick changes between various colours and/or EVA glue.
Executed according to model and version with roughing, individual face, bevel and radius cutters, rounding group, radius and face scrapers, sanding units, ....
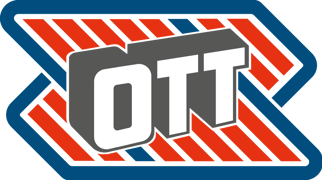
Machines for edgebanding have been DB&S's trump card for years.
With OTT, we have the top performer in this field available.
Austrian top quality where every machine is hand-made according to your wishes.
FlexEdge Technical data
Would you like to receive more information about FlexEdge?
Follow our latest news!
- Inspiration and ideas
- Always the latest updates on our machines
- Details about our info days and evenings