EXTREME ULTRA
Back to overviewNesting CNC technology without compromise, that's what the Extreme Ultra stands for. With its very spacious standard design, it is accessible to anyone looking for a heavy-duty nesting CNC machine with the necessary power and profitability. Coupling nesting technology with top performance, the Extreme Ultra succeeds wonderfully.
This machine can become the heart of your machining operations in your workshop. The highly intuitive user-interface with logical arrangement of controls ensures flawless integration into your operation.
Control via external CAD/CAM systems can be perfectly integrated. Automating or integrating into existing already automated production environments is no problem. Reliable, powerful and modern high-tech even for heavy work and yet individually and customisable if required.
Key highlights at a glance
- Gantry design
- Available working field dimensions: 1325 / 1336 / 1632 / 1640 / 2128 / 2132 / 2136 / 2142 / 2157
- Work areas divisible up to 18 vacuum zones
- Very easy-to-use operating software
- Automatic centralised lubrication
- Automatic tool length measuring system
- Wide range of automation possibilities
- Unbeatable value for money

AES machines are characterised by extremely solid construction and use of the latest technologies.
Thanks to the wide range, there is the right machine for every application.
EXTREME ULTRA Technical data
EXTREME ULTRA: Details
The central lubrication system provides various guides with a controlled dose of lubricant.
Periodic lubrication increases the lifespan.
This helps prevent malfunctions and boosts productivity.
With this handheld terminal, you can manually move the three axes individually using the handwheel at three different speeds.
An emergency stop button is also provided.
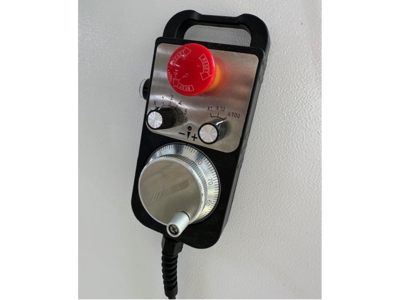
The handheld terminal is used to control the machine axes outside the control
panel in manual mode. Machine operating speeds and parameters can be
controlled with the help of the terminal. In addition, with the help of a handheld
terminal, general commands can be controWith this handheld terminal, you can independently move the three axes with infinitely adjustable speed using a potentiometer while running a program.
If the CNC machine is equipped with a Label X station, its speed can also be infinitely controlled via a second potentiometer.
Additionally, in manual mode, some general commands can be controlled outside the control panel, such as tool changes, vacuum pumps, and the position of the extraction hood.
An emergency stop button is also provided.lled with the help of tool change,
vacuum zone control & dust collection.
.png?width=400)
This CNC machine can be equipped with different types of milling motors with ceramic bearings, available in air- or liquid-cooled versions:
• 9 kW (12 HP), ISO-30 / HSK-F63
• 12 kW (15 HP), HSK-F63
• 14 kW (19 HP), HSK-F63
All types of milling motors are equipped with a pneumatically height-adjustable extraction hood.
Depending on the number of tools in your workshop, you can equip your CNC machine with an 8-, 12-, or 16-position rotary tool changer.
The rotary tool changer moves along the X-axis, and all positions are equipped with an anti-crash control sensor to ensure a smooth tool change.
The machine is standard equipped with a preparation to manually pick up aggregates in pre-set positions, in accordance with the selected aggregate with a specific operation.
The double pressure roller over the entire machine depth!
These pressure bars push your panel firmly onto the spoil plate. This is used when working in package (e.g. 3 panels on top of each other) and with very porous panels.
The automatic control of the extraction nozzle alternately allocates the full extraction power to either the drill head or the milling unit, depending on the active unit.
This ensures an optimal and efficient extraction result.
The High Flow matrix grid table is made of wear-resistant HPL (High Pressure Laminate).
The 30 x 30 mm grid is equipped with additional grooves that ensure a higher vacuum flow, resulting in optimal fixation of your workpieces.
This matrix grid table also allows working with specific vacuum cups, providing greater processing flexibility.
Multiple vacuum zones are automatically controlled according to the size of the panel.
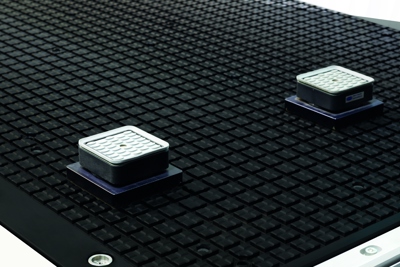
A user-friendly 21" flatbed color screen and all essential control buttons, integrated into the compact electrical cabinet of the CNC machining center, provides the operator with direct control and monitoring of the machine functions.
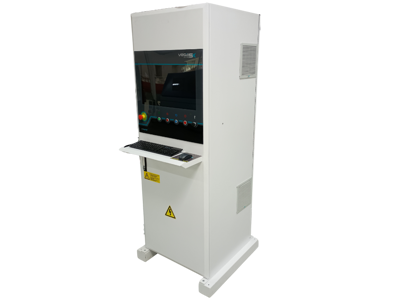
The modern, ergonomic, movable flatbed control console integrates both a 21” color screen and all essential control buttons.
The machine status is clearly indicated by large side LED color strips.
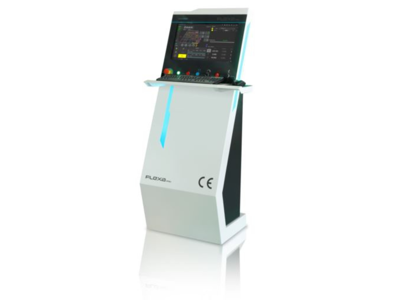
When entering the length dimension of new or re-sharpened tools, the machine places the tool on a calibrated measuring surface.
The measured actual value is compared with the theoretically entered value and is automatically adjusted in the tool library.
This results in highly precise machining operations.
.png?width=400)
This CNC machine can be equipped with one or more vacuum pumps.
The available options are:
• 140 m³/h
• 250 m³/h
• 300 m³/h
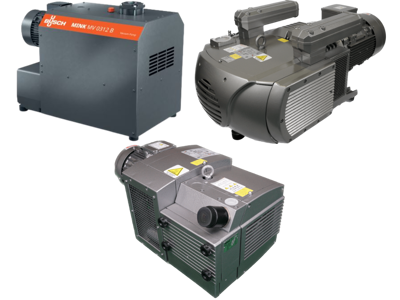
NC Hops CAD/CAM user interface in combination with the AES PLC for axis control.
Easy graphic programming of workpieces.
Graphic representation of workpiece, machine details, clamps, ect possible.
Import of .DXF, .STL, .STEP drawings possible.
Including 3-D simulation and collision
control
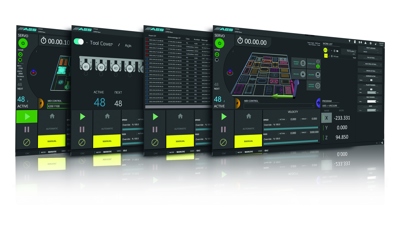
The sensors in the stop cylinders provide additional control over their height position.
This results in an even safer machine environment at all times.
The operator can easily control the machine via a 21" touchscreen. This screen supports the physical buttons and provides a visual and intuitive way to enter machining programs, adjust settings, and monitor the machine.
Closed cable chains ensure that dust and chips are kept out of the cable chain.
This provides extra protection for the electronic cables inside the cable chain against aggressive dust released during the processing of special materials.
Extra protection for guides and bearing blocks through an additional seal mounted on the bearing blocks, which retains the lubricant better inside the bearing block and keeps dust out more effectively.
A barcode scanner on a CNC machining machine is used to quickly and accurately select workpieces in a program database. By scanning barcodes, the correct machining information is automatically loaded, reducing errors and increasing efficiency. This contributes to an automated and streamlined production process.
A manual labeling unit on a mobile control console of a CNC machining center is used to manually apply labels to workpieces. This ensures clear identification and traceability within the production process, reducing errors and increasing efficiency.
Consists of an additional touchscreen for workpiece selection and a label printer.
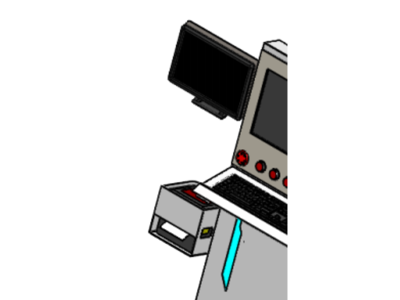
The tool is cooled using compressed air during the machining of specific materials such as plastic, aluminum, etc.
This improves machining quality and extends the tool's lifespan.
The C axis also called fourth axis.
This allows automatic rotation of an aggregate from 0° to 360°, including 4-axis interpolation.
An additional second zero point at the front right is extremely practical for positioning smaller workpieces on the machine table.
Includes additional stop cylinders and software adjustment.
The vacuum zones of a CNC nesting machine are designed according to the work area dimensions and the most common sheet formats, ensuring both large and small sheets are securely and efficiently held in place.
The VACUBOOST system uses two vacuum pumps. The first pump keeps the workpiece securely in position. During machining, the milling cutter moves across the table from one vacuum zone to another.
The second pump, through the intelligent VacuBoost system, provides an additional concentrated vacuum precisely where the milling head is performing the operation.
This horizontal light curtain detects interruptions in the light beams and stops the machine when an object or person is detected.
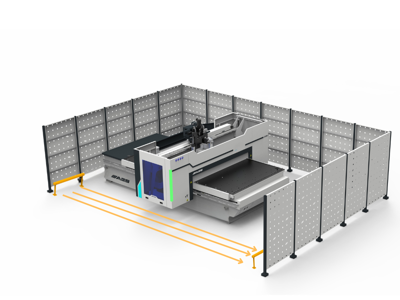
A light curtain is a safety feature consisting of a transmitter, a receiver, and non or multiple mirrors, which together create an invisible safety barrier around the machine.
This light curtain detects interruptions in the light beams and stops the machine when an object or person is detected.
.png?width=400)
The fencing provides a robust enclosure on maximum of 3 sides of the CNC machining center.
The open side is equipped with another safety system of choice, in according with CE regulations.
This prevents the operator from unintentionally entering the danger zone of the machine.
Of course, it is possible to provide a safety door in the fence to allow controlled access to the machine.
Pressure cushions, at the front and/or rear, of the CNC machining center serve as an essential safety system.
When touched, they detect the presence of a person or object and immediately stop the machine.
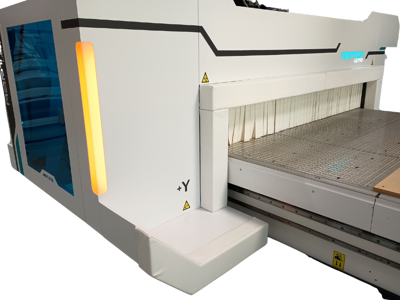
A security system with a zone scanner is an advanced safety solution for CNC machining centers. The scanner, mounted on the chassis, detects people or objects within the safety zone of the scanner. This ensures a safe working environment without physical barriers, improving accessibility and efficiency.
A solid table on the infeed side of the nesting cnc machining centre equipped with an HPL top.
This table is suitable for plate per plate loading, manual or an automatic system.
A full pack of panels can be easily placed on this hydraulic lift table using a forklift, thanks to the cross beams.
Multiple alignment stops with steel rollers in the Y-direction and a corner stop ensure precise positioning of your panel for processing.
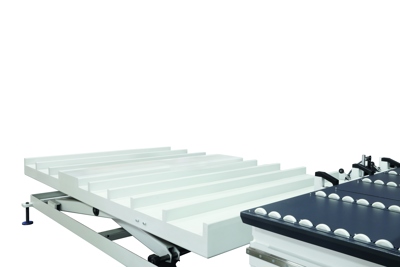
Label X is AES' combined alignment and labelling station. This system precisely positions the plates on the infeed table before applying a personalised label in the correct location. This dual functionality optimises both positioning accuracy and plate traceability in the production process.
Thanks to the alignment robots, the alignment process runs smoothly without operator intervention.
The robots ensure that the panel is precisely aligned against the vertical studs with steel rollers.
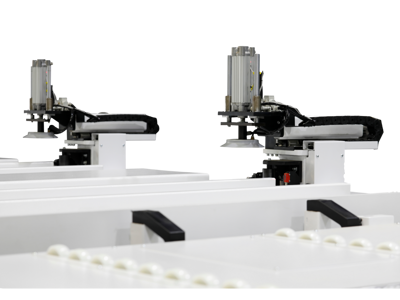
The loading unit, mounted on the machine bridge, transfers the panel from the infeed table to the nesting table using multiple vacuum suction cups. This ensures a smooth material transfer within the CNC nesting machining center.
After machining, the push-off and cleaning unit (mounted on the the machine gantry) removes dust from the workpieces and transfers them to the outfeed conveyor.
The conveyor belt transports finished parts from the machine to the operator.
This ensures the efficient and orderly disposal of parts, keeping the production flow running smoothly.

The label printer at the outfeed conveyor is used to manually apply labels to workpieces. This ensures clear identification and traceability within the production process, reducing errors and improving efficiency.
Consists of an additional touchscreen for workpiece selection and a label printer.
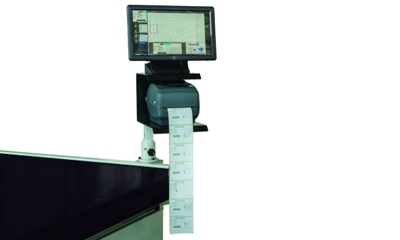
Would you like to receive more information about EXTREME ULTRA?
Follow our latest news!
- Inspiration and ideas
- Always the latest updates on our machines
- Details about our info days and evenings